Advanced technology and sophisticated equipment, combined with decades of knowledge about natural stone products, allow us to offer high-quality product lines, consistent with international standards.
The spirit of innovation and understanding of natural stone run deep at Xpereos. Quality is at the core of all our processes – from quarrying, to hand splitting, to sawing. We offer multiple finishes and follow international packaging standards for all our products.
Infrastructure
Our continuous investments in new product development has given us the ability to offer advanced solutions to support any design vision of an architect or home-owner
It is our constant endeavour to invest in state-of-the-art machinery and equipment to increase efficiency and new product offerings to our customers. We provide regular training to our production division. The highly skilled team are adept at using the sophisticated manufacturing technologies available in-house.

State-of-the-art Equipment for Cutting & Finishing
With our high-end international machinery, we achieve exacting results for cutting, calibration and finishing.
Jumbo block cutters for extremely large stone pavings
Mono block cutters for efficient cutting of thick slabs
A range of premium finishing machines including flaming, water blasting, line polishing, antiquing and shot blasting
Bullnosing machines and bridge saws for efficient cutting
Premium CNC cell with Italian machines for cutting diverse shapes

Total sawing capacity
2,50,000 sq. m
Total Calibration capacity
30,00,000 sq. m
Quality Checks
Quality inspection at every stage ensures dimensional accuracy of each natural stone slab
The quality process starts at the quarries by choosing an ideal location with sophisticated mining capabilities to extract as per project specifications. The selection of a particular spot for quarrying is a skill that our seasoned team is well versed with. Precise cutting to specifications, the right finishing to enhance the stones and packaging to international standards are done with quality checks at every stage.
Quarrying
We extract more than 550k ft3 of raw material from our own and partner quarries in India.
Cutting
After this primary cutting stage, we primarily use bridge saws for secondary cutting. Our experienced technicians along with our automated machinery ensure straight lines and timely dispatch at every stage.
Finishing
At every stage of the production process, the product is checked against quality control samples. In addition to matching it with samples, photographs of each batch are taken to check for consistency.
Packaging
Our focus on sustainability has led us to minimize the use of styrofoam and wood without compromising on the sturdiness of the packaging.
Reporting
In addition to matching final supply with samples, photographs of each batch are taken to check for consistency. Stringent accuracy norms for minimal accepted variation and zero-defect in stone surfaces is at the core of every step of the process.
Safety Measures
We follow the highest standards of safety and provide regular training on equipment handling to all shop floor employees.
A safe work environment at the quarries and factories is critical for us. We have invested in building awareness and identifying workplace hazards, and countering them with effective measures to ensure a safe and healthy working environment for our employees. This includes implementing safety programmes with training, providing safety gear and equipment, reporting unsafe incidents and providing mechanical aids at the shop floor.

Signages on the
shop floor

Non – Slip
Industrial Floors
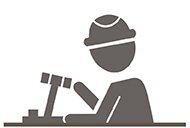
Equipment
Usage Training
